製造工程の見直しでコストダウンに成功
ご要望
「材料費が高騰してしまい、既存の取引メーカーの製造コストが上昇して困っている。何とか解決できないだろうか?」
POINT
- 長年培った知識、技術、ノウハウを持つスタッフによる徹底的なヒアリング
- 余分な工程の洗い出し
- 製造・加工設備をもつ充実した工場による作業工程の自動化により、工程削減
完成までを振り返って
依頼のあったアジャストボルトは、六角ボルトで頭部が丸みを帯びた形状のねじ。
丸みの部分を綺麗に保ちつつ、コストダウンを実現し量産までおこなった過程を振り返ってもらいました。
―どういった経緯で依頼をいただいたんですか?
「ねじの頭の丸い箇所は、当初、切削でおこなっていたそうです。 切削で綺麗に削るとなると、当然手間がかかるわけですが、そこをなんとかコストダウンできないかということで相談をいただきました。」
「コストダウンするなら、冷間加工でやるべきやと。ただ、うちでも冷間で“丸みを出す”というのはやったことがなかったんでね。“やってみな分からん”ということで、まずはホンマにできるかどうか検証するところからのスタートですわ。」
―苦労されたことなんかはありますか
「簡単に言うてくれるけど、そりゃ苦労ばっかりですよ。」
(笑)
「やっぱりねじの(頭の)”丸み”が課題になった。
冷間加工は金型の底に空気が溜まってしまうから、上手く丸い形状にならず苦労しましたね。」
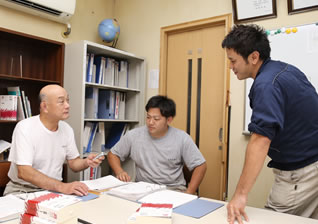
「それで、穴を空けて底に溜まった空気を抜いてやればいいんじゃないかと。 で、型を何回も何回も修正して。出来た!と思ったら、今度は空気の圧力で割れてしまった。」
「いろんな方法でやってみたんやけど、結局は基本に戻って金型自体の精度を上げようということになったんですよね。靱性を持たせて割れにくくしたり、強度を上げるにはどの硬さがベストなんかを何回も試しました。」
「組み合わせは何種類もやったし、焼き入れの硬さ調節もたいへんやった。
ダイス鋼で金型を作って、量産もうまくいったし、いやー完成してほんまによかったわ。」
―最後に、この仕事を通じて感じられたことを・・・
「お客さんも喜んでくれはったし、それがなによりかな。 やっぱり、難しくても”やってみよう”というチャレンジ精神が大事やな。」
「ほんまにそうですね。人が「できない」と言ってることでも、やってみる価値はあるなと思いました。
それに、金型造りがいかに重要か、いつも新しい発見があるのはおもしろいんですわ。」
「お客さんのおっしゃってたコストダウンに成功したし、僕は、ここにきて5年になるんですけど、
”よそにできんねじを作ろう”っていうのが、やっぱりうちの良い所やと改めて思いました。」
皆さん、ありがとうございました!
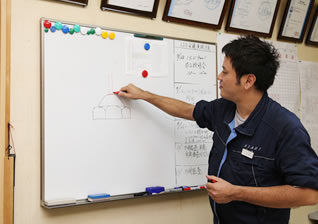